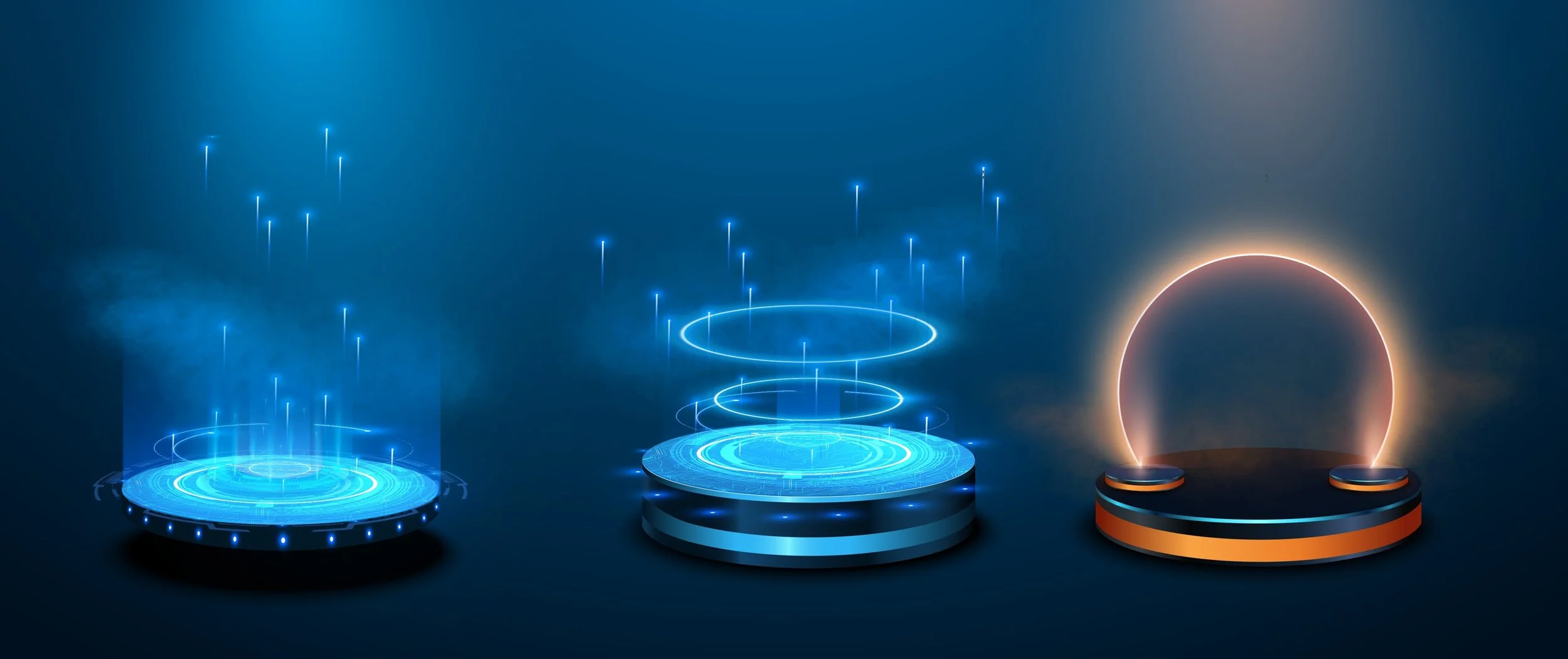
Technology Platforms / Custom Fabrication / Thermal / Thermal Management
Thermal Management
3DGS thermal designs constructed of high-efficiency copper allow scalability and flexibility with compact designs that offer thermal transfer of up to 100 W/m-K.
Improved Heat Dissipation and Thermal Cycling
100% copper system minimizes stress on solder joints over repeated, long term, thermal cycling.
IMPROVE PERFORMANCE AND REDUCE PACKAGE SIZE
Heat spreaders and heat sinks from our unique mini pin fin manufacturing process enable designers of small electronics to build more compact packages.
Heat spreaders and heat sinks made in 100% copper can be made as small as 1mm x 1mm, and as thin as 200 microns, enabling truly small packages.
100% COPPER ENABLES BETTER PERFORMANCE
Copper has a higher thermal conductivity and conducts heat faster than aluminum. Therefore, the temperature across the heat spreader OR heatsink will be more uniform. With a higher volumetric heat capacity than aluminum, it takes a larger quantity of energy to raise the temperature thus smoothing out the thermal load.
Copper heat sinks and heat spreaders better match the CTE of the solder joints which reduces fatigue failure from repeated, long-term thermal cycling. However, copper has a higher density and is traditionally more expensive than aluminum.
Heat sinks and heat spreaders from 3D Glass Solutions, with the mini pin fin design, leverage the advantages of the copper and minimize the disadvantages (weight and expense).
100% copper heat spreaders outperform copper ‘coin’ designs as the mini pin fin’s internal structure enables torsion relieving stresses from thermal cycling.
Additionally, copper heat sinks and heat spreaders can be designed to integrate I/O signals within the package, enabling more functionality in a smaller footprint.
ULTRA SMALL DESIGNS FOR ULTRA SMALL PACKAGES
50 micron mini pin fins enable effective thermal transfers of up to 100 W/m°C. This is far superior to the single piece copper coin solution which is limited by its inherent surface area.
Traditional productions methods in the past have not been able to cost-effectively produce efficient AND small heat spreaders and heatsinks.
CUSTOM SOLUTIONS FOR IMPROVED OUTCOMES
Each application is unique in footprint, thermal management requirements, and additional features. Contact us directly with your specific needs.
PARAMETERS | TYPICAL |
---|---|
SIZE | 5mm x 5mm |
HEIGHT | 250µm |
MINIMUM PIN-FIN SPACING | 50 – 200µm |
MINIMUM PIN-FIN DIAMETER | 50 – 100µm |
Applications
RF amplifiers
GaN amplifiers
GaAs amplifiers
LDMOS amplifier
LED
LCD
Small electronics with heat management challenges